How to Repair an FRP Tank
- PlasTech Services Inc.
- Nov 2, 2022
- 3 min read
Updated: Jan 26, 2024
FRP TANK REPAIR
Chemical distributors, Water Water Treatment Facilities, and similar industrial operations can discover fiberglass storage tanks with degradation, cracking, and delamination of the fiberglass due to chemical and UV exposure.
Get in Touch with Us: 1-410-737-4700

Inner linings, side-wall delamination, manways, roof areas, floor areas, nozzle attachments, and other penetration locations can become the most critical areas identified for repair. In
addition, the vent piping on top of the tanks may need to be replaced. If the structural integrity remains intact, facility engineers and maintenance managers can skip the stress of replacing FRP Tanks and request a free quote for an FRP Tank repair or reline.
We can provide high-strength, chemical-resistant fiberglass repairs and a wax coating to prevent further degradation. We will sand the fiberglass, grind any cracks or holes to the appropriate layer, fill and repair, and reline the tank's inner walls.
WHAT IS FIBERGLASS-REINFORCED PLASTIC USED FOR?
Fiberglass-reinforced plastic (FRP) is often used for bleaching applications in the pulp industry, caustic processing in the chemical manufacturing industry, and wastewater treatment in the water treatment industry. It is commonly used for chlorine dioxide, sodium hypochlorite, filtrates, caustic, wastewater, and effluent applications.
The design of this equipment employs an inner surface of the FRP called a corrosion barrier to protect the load-bearing structural elements of the asset from the fluids contained. Conventional practice is to monitor the condition of the corrosion barrier and assume that as long as the corrosion-resistant layers are intact, no damage occurs to the structural layers.
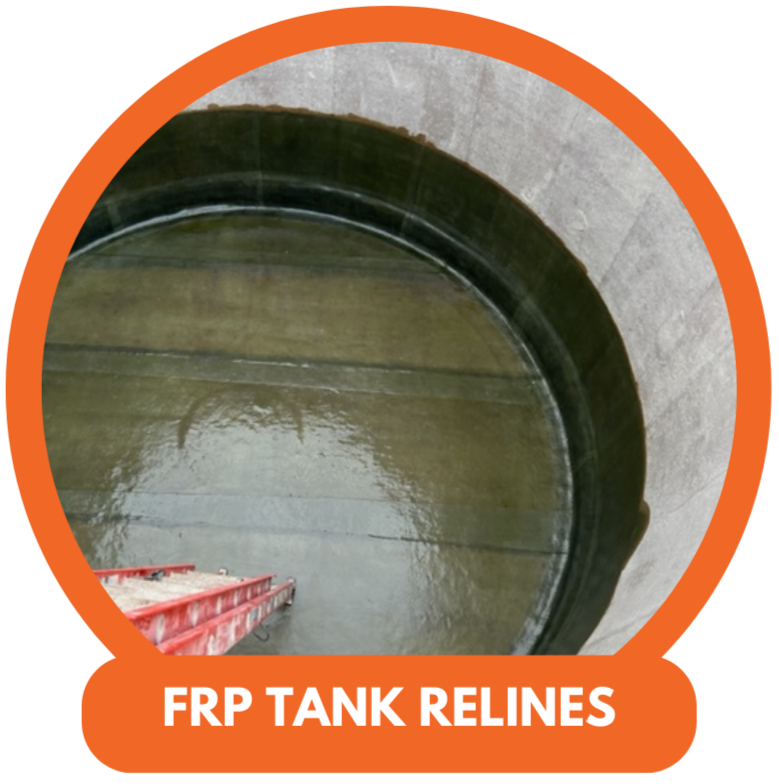
Fiberglass Reinforced Plastic (FRP) is widely used for tanks, scrubbers, pipelines, and other paper, power, and chemical equipment for corrosion resistance at moderate temperatures.
FRP is used in several applications in the pulp bleaching process, as well as for handling and storing other chemicals used throughout papermaking. Typical applications include bleach filtrates, filtrate tanks, chlorine dioxide handling, D-stage pre-tubes, and stock lines.
FRP is a composite material because it is a mixture of several component materials. In addition, the material can be assembled in several ways within the same structure or equipment to suit individual applications.
UNDERSTANDING FRP AND CHEMICAL RESISTANCE
Chemical resistance with FRP comprises four primary materials - resin, glass, mat, and a wax coating.
Resin is the most common material associated with FRP. It isn't easily manufactured and is easily susceptible to supply chain issues. It functions as a glue that binds the structure to form a leak-tight containment and provides a significant portion of the corrosion and chemical resistances in FRP Tanks.

FRP forms both a structural material and a corrosion-resistant material. In the industrial industry, FRP is used successfully for storage tanks, process lines, scrubbers, washer hoods, tank linings, and piping. FRP is lighter than stainless steel, easier to repair, and doesn't require hot permits.
The glass/resin layers can be changed through the thickness, and the glass fiber orientation can be modified to provide specific structural properties. Fiberglass can also be customized to fit a particular dimension or structure.
Resin + Fiberglass Layers + Wax Coating = Chemical Resistance. Notably, the kind of chemical used in the FRP Tank will determine the type of resin used in the repair or reline.
WHY DO FRP TANKS NEED REPAIRS?
FRP Tanks can gradually lose chemical resistance due to the oxidation of the corrosion barrier surfaces. Small cracks in the corrosion barrier can appear, leading to a deeper chemical penetration, thus compromising the corrosion barrier. The chemicals can also attack the corrosion-resistant layer of resin because of their toxic structure or temperature f
rom a chemical reaction. The tank walls can also form blisters, Air Bubbles, Chips, Cracks, Crazing, Deformations, Delamination, Dry Spots, Edge

Delamination, Foreign Inclusions, Pitting, Scratches, Surface Pinholes, and Wrinkles.
Failing FRP Tanks can lead to containment failure. Containment failures can also result from blond failure, flange failure, nozzle failure, manway failure, or impact damage (e.g., forklift hitting the tank).
A Thorough tank inspection needs to be completed. Check out our Tank Inspection Guideline by clicking here.
FRP TANK REPAIR FROM OXIDATION
Oxidation of corrosion barrier surfaces occurs because the resins used in FRP are organic polymers, which can be oxidized. When oxidizing agents such as sodium hypochlorite (hypo), chlorine, and chlorine dioxide are contained, oxidation of the resin will occur. When these substances are contained, an FRP corrosion barrier must be considered sacrificial. We recommend an FRP Tank inspection every five years to ensure corrosion resistance and integrity.
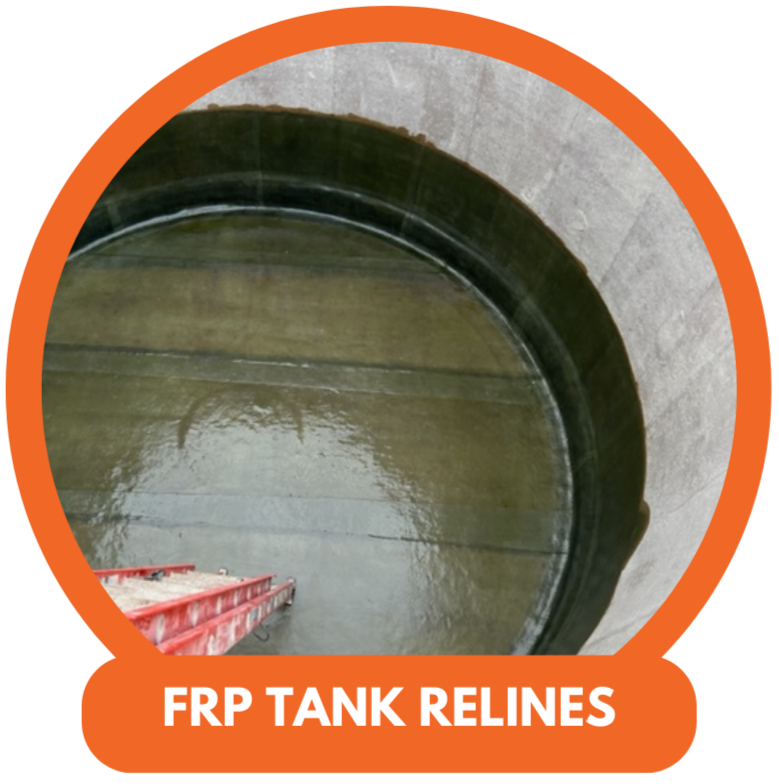
Oxidation is relatively easy to detect visually. The surface will be yellowed and lose its shine. The oxidized resin on the surface is softened and can be abraded off with little effort.
Oxidation reduces the thickness of the corrosion barrier. In cases where oxidation occurs, the total thickness of the FRP will reduce.
We specialize in FRP Tank Repair, FRP Tank Inspections, and FRP Tank Relines. For a no-obligation free quote, submit a request online, call 410-737-4700, or email us at contact@plastechservices.com
Comments