All you need to know about plastic welding repair services
- PlasTech Services Inc.
- Dec 18, 2022
- 2 min read
Updated: Dec 20, 2022
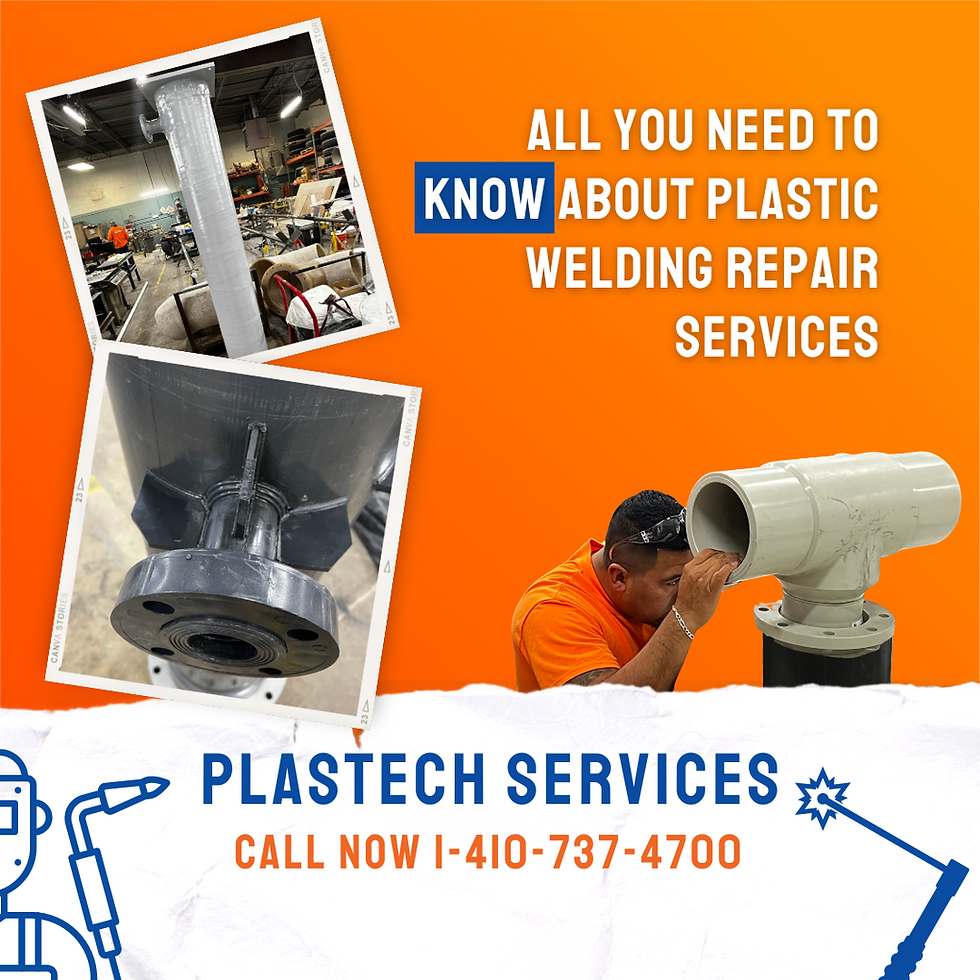
Plastic Welding Repair Services
Plastic welding repair services are quickly becoming a sought-after, cost-effective, and reliable solution for industrial businesses looking to maintain and improve the performance of their machinery and equipment. This article provides a comprehensive overview of plastic welding repair services, including their benefits, the processes involved, and the types of materials they are suited to.
What is Plastic Welding Repair?
Plastic welding repair is a cost-effective and reliable means of restoring machinery and equipment in industrial environments. It involves using heat and pressure to melt two pieces of plastic together, resulting in a strong bond that can withstand heavy wear and tear. The process is suitable for a variety of plastic materials, including polyethylene, polypropylene, polyvinyl chloride (PVC), polycarbonate and other engineering plastics.
Benefits of Plastic Welding Repair Services
Plastic welding repair services offer a number of advantages over traditional welding techniques. Firstly, they are more efficient than traditional techniques as they involve minimal preparation time and require less energy to complete. Additionally, plastic welding repairs are much more economical than other processes as they do not require expensive materials or complicated tools. Finally, plastic welds are extremely strong and durable, making them ideal for use in highly demanding industrial environments.
Processes Used in Plastic Welding Repair Services
Plastic welding repairs are usually completed using one of two processes: hot gas welding or hot plate welding. Hot gas welding involves using hot air to melt two pieces of plastic together while hot plate welding uses heated metal plates to heat the plastic before fusing it together. Both processes require a skilled technician to ensure that the weld is successful and free from defects.
Types of Materials Suitable for Plastic Welding Repair Services
Plastic welding repair services can be used on a variety of materials, including thermoplastics such as polyethylene, polypropylene and PVC; thermoset plastics such as epoxy resins; and engineering plastics such as fluoropolymers and polycarbonate. However, it is important to note that different materials respond differently to the heat used during the plastic welding process; therefore it is essential that the technician is familiar with the material being used before proceeding with the repair.
Five Important Insights for The Industrial Industry
1) Plastic welding repairs are becoming increasingly popular in industrial environments due to their cost-effectiveness and reliability.
2) The process requires minimal preparation time and less energy than traditional welding techniques.
3) Plastic welds are extremely strong and durable, making them ideal for use in highly demanding industrial environments.
4) Different materials respond differently to heat during the plastic welding process; therefore, the technician must be familiar with the material being used before proceeding with the repair.
5) Careful consideration must be given when choosing a plastic welding service provider; it is important to ensure they have experience working with a wide range of materials.
Request A Free Quote
As certified plastic welders, we can provide a no-obligation free quote for your project at www.plastechservices.com/quote or call us at 1-410-737-4700.
Comments