
We repair and customize plastic tanks, pipes, and custom-designed equipment
We are certified in plastic and thermoplastic welding, fusion, and repair services. Our expertise includes custom fabrication, tank repair, and pipe installation with a specialty in chemical-resistance.
​​
-
Propylene (PP): This versatile, FDA-compliant material boasts high resistance to moisture absorption and offers superior chemical resistance.
-
Polyvinylidene Fluoride (PVDF Kynar): A highly inert thermoplastic fluoropolymer & excellent chemical resistance against halogens.
-
Teflon (PTFE): Non-stick properties, PTFE offers outstanding chemical resistance and performs well across a wide temperature range.
-
High-Density Polyethylene (HDPE): HDPE is a durable, versatile, and cost-effective material with excellent resistance to abrasion and chemicals.
​
Need help with custom fabrication or repair? Fill out the form and we'll be in touch!
Our Plastic Welding Serivces
-
Leak Repairs: Addressing leaking plastics and broken pipes by establishing waterproof or airtight seals.
-
Dual Containment Systems: Designing and creating advanced dual containment systems.
-
Tank Repairs and Installations: Specializing in the repair and installation of various plastic tanks.
-
Custom Fabrication: Crafting thermoplastic equipment parts and fixtures tailored to specific needs.
-
Containment Solutions: Developing trays and systems to manage chemical overflow effectively.
-
Butt-Fusion Welding: Utilizing heat fusion techniques to join thermoplastics like polypropylene, creating strong, leak-free joints without the need for fillers.
Understanding Plastic Welding
Plastic welding involves creating a molecular bond between two compatible thermoplastics, resulting in superior strength and reduced cycle times. The process comprises three main steps:
​
-
Pressing: Aligning and applying pressure to the materials to be joined.
-
Heating: Applying heat to soften the materials at the joint interface.
-
Cooling: Allowing the materials to solidify, forming a strong, cohesive bond.
Various heating methods differentiate plastic welding processes, while the application of force and cooling allowances vary based on specific machinery and techniques. Check out our video answering the question, "What Is Plastic Welding?"
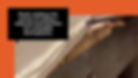
Butt-Fusion of Polypropylene Pipe
Butt-fusion, or heat fusion, is a technique used to join thermoplastics like polypropylene. This method involves heating the ends of pipes and pressing them together, forming a bond as strong as the original material. Unlike other methods, butt-fusion doesn't require fillers and maintains the integrity of the connection, reducing the likelihood of leaks or failures.
​
If you're seeking an industrial services partner for custom chemical trays, plastic tank repairs, installation of polypropylene pipe, or any chemical-resistant related services get in touch with us!
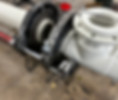
Chemical-Resistant Trays

Responding to the increasing demand for chemical-resistant solutions, we have developed specialized trays designed to contain spills and prevent environmental contamination. These trays are fabricated from materials like Polypropylene and HDPE, chosen for their robustness and resistance to a wide range of chemicals. Our custom-designed trays are suitable for various industrial processes, including chemical processing, pharmaceutical manufacturing, and food production, providing a reliable solution for spill containment and equipment protection.
Custom Fabrication and Repair Services
Our team excels in the custom fabrication of thermoplastic equipment, including the design and construction of chemical-resistant tanks, containment trays, and processing equipment. Utilizing advanced plastic welding techniques, we ensure that each component meets stringent quality standards and is tailored to the specific requirements of our partners.
Additionally, we offer comprehensive repair services, addressing issues such as leaks or structural damages, thereby extending the lifespan of your equipment and minimizing operational disruptions.
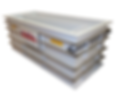.png)
Chemical Resistance in Industrial Applications
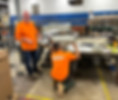
In industries where exposure to aggressive chemicals is prevalent, selecting the appropriate plastic material is crucial. Materials such as Polypropylene (PP) and High-Density Polyethylene (HDPE) are renowned for their exceptional chemical resistance, making them ideal for applications involving acids, alkalis, and other corrosive substances. These materials not only withstand harsh chemical interactions but also offer durability and longevity in demanding settings.
Material Selection and Expertise
Selecting the appropriate material is a critical aspect of our service. We consider factors such as chemical compatibility, operating temperature, mechanical load, and environmental conditions to recommend the most suitable plastic for your application.
Our extensive experience and comprehensive database on the chemical resistance of plastics enable us to provide informed guidance, ensuring that the chosen material offers both performance and cost-effectiveness.
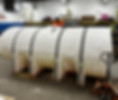